MONDAY - We spent today installing the floor heating pipes in the basement. Jay and Mr.W laid them all out in the different zones, keeping them to the right lengths, and I followed behind and zip-tied all the pex pipe to the rebar. I am really excited about what the basement floor will look like in the end and with the pex pipe, the floor should be comfortably warm!
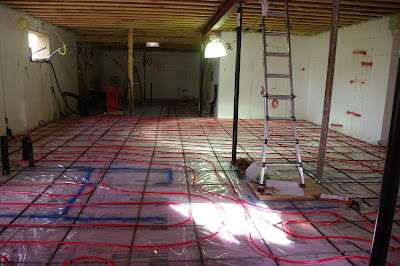
TUESDAY - Today was supposed to be the day the fireplace was installed. We found out in the morning that the installation would not be happening due to a missing piece. It was a little frustrating since the nights are getting cooler and we were anticipating using the fireplace for heat. We will have to wait a little longer. Even though the fireplace could not be installed, it was delivered so installation should happen sometime this week. Since the nearly 600-lb fireplace arrived, we decided to install the front doors. We were waiting for the fireplace to come in so we wouldn't wreck the doors or the threshold. It is a beautiful set of glass doors so we wanted to make sure to put them in after all likelyhood of damage would occur. Plus, it is getting chilly in the house and closing up the front door opening makes a huge difference. It was fairly straightforward. We didn't put the proper hardware on the door just to make sure that isn't damaged so we put on another locking set. It is so fun to walk in and out of the front door and listen to how it clicks closed so nicely. The kids enjoy going in and out, too.

While we were in the door installation process, Mr.W also installed the house-to-garage door, which is just a steel 6-panel door. That keeps that end of the house significantly warmer as well. While Mr.W was installing the garage door, we were busy insulating (insulation = "air pouffalation" according to our 3-year old) and putting up poly in the garage ceilings. The drywall crew wanted to get in to put the first layer of ceiling drywall in this evening so we needed to get moving. Finally, Mr.W started the bulkheads in the diningroom area. I think the traditional way of framing bulkheads is to use all-wood construction but we have been using metal angle pieces and small 2x4s instead. It comes together very quickly and once the drywall is attached, you would never know it is not all-wood.
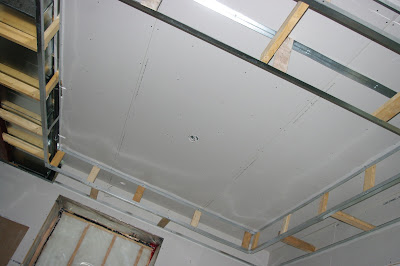
WEDNESDAY - This morning I arrived early to help with the pour of the concrete floor. The kids stayed at grandma/pa's overnight to accommodate the early morning so I didn't need to worry about them. Pouring this floor was so much easier and so much more relaxed then when we poured the garage floor. It was a nice cool morning with a little bit of rain - perfect concrete setting temperature. Jason did the hardest work by manning the big tube from the concrete pump. The concrete pump parked in front of the garage and then snaked the hose around the front of the house and into the basement window. That hose is thick and heavy and requires a lot of strength. Jay did a great job. While he poured the concrete we raked it around to the edges, bringing it just up to the chalkline we snapped earlier to show us the final height. We also cut some 2x4s to the exact distance between the bottom of the floor joists above and the height of the concrete below. Simply by holding that 2x4 on the bottom of the floor joist we knew if the concrete in each area was too low or too high. When an area was full of concrete, Mr.W worked the power screed and screed the floor. The pour was rather uneventful (there was a time when the concrete got stuck in the tube and it required a bit of work on the part of the operator to get it flowing again) and it went off rather easily. After the pour was done, Mr.W and I worked on the finishing of the floor. He used the power trowel to work the main areas and I used a hand trowel to work the edges. Over and over, around and around we went. Eventually Mr.W kicked me out of the basement and he finished it off. It took longer to harden than we anticipated (even though we added accelerator) but the finish looks really nice. Once again, I look forward to seeing the finished concrete floor after the decorative technique we will be applying but we need to wait at least 28-30 days before we can do that.
![]() |
Concrete basement day after pouring |
Once the basement was done, Jay worked on insulating the garage walls and putting up the poly and I made the bulkheads for the livingroom. I really enjoyed making the bulkheads. It requires some precision and I like that! Plus, they are going to look fantastic when they are done!

THURSDAY - I was gone for most of the day today so I wasn't sure exactly what Jay did. I know he covered all the upstairs windows with plastic to prepare for priming the drywall. We will be spraying the walls and ceilings and we don't want the windows painted. I had to go to a doctor's appointment to check on the status of my eye (the ulcer is gone but there is still some swelling. Bad news is I cannot wear contacts for at least 1 month! That sucks.). Since I was going to be gone I took Ari with me and we had a little date time. We went out for lunch, did some shopping and I picked up the paint for the ceilings and the trim work. 5 gallon pails of Benjamin Moore paint are not cheap! But it will be worth it! When I got back in the later afternoon, I finished up the bulkheads in the livingroom while during the day the drywall crew boarded the bulkheads in the diningroom. They look so good!
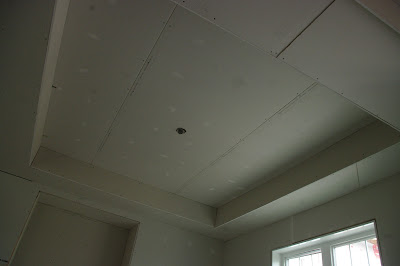
FRIDAY - Sometimes I like to arrive on site knowing what we will be doing and sometimes I like being surprised. Today I was certainly surprised. When I arrived, the guys were already working on the front porch roof. I squealed with excitement! So, I jumped in to help. I handed up the trusses to Mr.W who was waiting for them up top. He attached it and I handed up another. Over and over. Jay went to help work on the well head again to get that finished so he was occupied elsewhere. Not to underestimate the importance of what he has done, it is because of his work that the well work is complete and we will have water in the house (and in the trailer for now). Once about half the trusses were up, I started cutting 2x4s and 2x6s to make the overhang on the west side of the porch roof and all the blocking for between each truss so there would be additional nailing support for the OSB. Once they had all the trusses up and the blocking in place (Jay was done with the well by then), I started cutting OSB sheeting as Mr.W called out measurements. I cut the pieces, Mr.W tacked them in place and Jay followed behind to finish up the nailing.
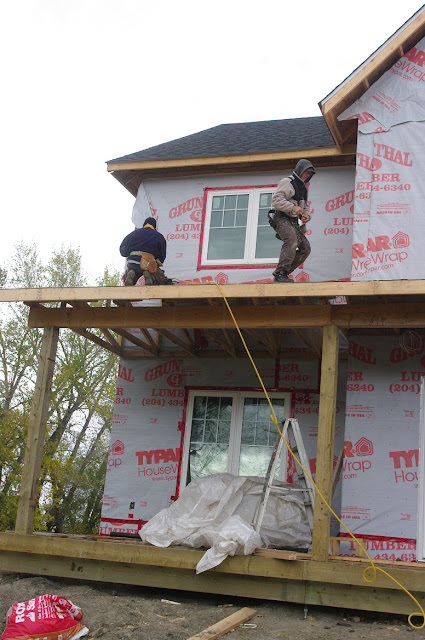
We have also hired another guy to help us (the other 2 guys we had went back to school) so he was helping me lift the OSB up to the porch roof and carrying the large 4x8 sheets for me to cut. It was NOT a lovely day weather-wise to be working. It was raining and then windy and then cold and then the sun would come out for a bit and then the wind would pick up again and then it would be cold and rainy again. There was even sleet for a little bit. But we persevered and finished it up, scrounging up pieces of OSB at the end but the framing of the porch roof is complete! It looks just like it belongs. I love the proportins of the house and I think each element works well together. I look forward to seeing the siding and trim boards in place. After a day like today, I really look forward to using the air massage tub and warming up in a nice hot candlelit soak but that day will come soon enough.
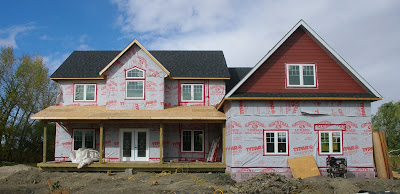
While we were outside in the cold, the WETT-certified installer was installing the fireplace. There must have been some challenges because 2 separate deliveries arrived for missing or wrong parts and in the end he is still missing parts to complete it. Once again we are frustrated but there is little we can do about it except to let the company know of our dissatisfaction. They knew long in advance which fireplace we were installing so there is no reason they should be missing parts or have the wrong ones. Hopefully early next week it is complete and we can use it.

The drywall crew was hard at work again boarding and starting to tape and mud the first floor. I believe most of the main floor is boarded save for a couple of livingroom bulkheads - the fireplace installer was using the livingroom space so the drywall crew couldn't get in there.
I want to say a little bit about the drywall crew we have hired. They are a fantastic husband/wife team who work well together and do a great job. When someone is in your house everyday for 3+ weeks, you get to know them a little. They are encouraging and honest and kind and keep good lines of communication with us and put up with our kids with gentleness -- I really appreciate them. They are so different, the two of them, but they love each other and support each other in their differences. I am very thankful to have them working for us.
Next week is the last week where I will be at the house everyday, all day. I need to start schooling and I will do that Oct. 1. I am hoping we have the priming of the second floor complete and the painting of the ceilings done by the end of this next week so I can start painting walls after that. I am not sure what the day will look like when I start schooling but I would hope to be done by about 3 in the afternoon so I can work on the house the rest of the afternoon/evening. We will see how it all turns out!